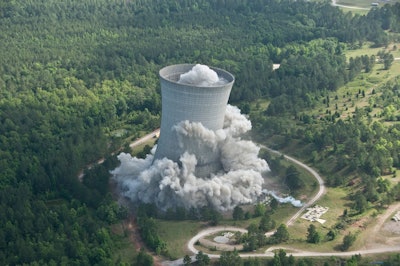
Bill Schaab had a lot of experience handling the kind of material most people run from when he started American Demolition & Nuclear Decommissioning in 2004.
When asbestos was identified as a health hazard, Schaab formed a business removing the insulation. He studied the regulations and became an expert in the field.
Fast-forward a decade, and he was learning how to handle another, more hazardous material, by decommissioning nuclear sites. The regulations were about three times thicker than those for asbestos. Schaab studied them and helped the company he was working for at the time win scores of projects around the country.
After becoming burned out from the constant travel and hectic schedule, he once again branched out on his own. He was later joined in the business by his cousin William Sundeen, who bought 51% interest in the company. A disabled veteran, Sundeen retired from a 22-year career in the Navy, where he specialized in nuclear weapons and material, to become the company’s president, CEO and treasurer.
Today, American Demolition and Nuclear Decommissioning travels the country and into Canada tearing down large contaminated structures. The projects often take years to evaluate for bid and decades to complete. But it’s a niche that Schaab and Sundeen feel comfortable in, as they both are sticklers for safety and procedures. They have become innovators in their field, engineering equipment to meet their needs and educating the radioactive-waste-management industry on the latest technological advancements.
They have also achieved an exemplary safety record, surpassing 750,000 work hours and 21 years with zero OSHA reportable incidents.
For this and more, American DND was named Equipment World’s 2025 Contractor of the Year, as well as the 2025 Safety Award winner, both presented March 21 during a ceremony at the Bobby Hotel in Nashville, Tennessee.
From left, Bill Schaab and Bill Sundeen, owners of American Demolition & Nuclear Decommissioning.Equipment World
Why Nuclear? … Why Not?
Schaab was working for Demco Inc. in Buffalo in 1997 when the company got a tip about an RFP to tear down a radiologically contaminated building in St. Louis.
By then, Schaab had years of experience in demolition and handling hazardous materials. Demco’s owner asked Schaab to review the RFP over the weekend and let him know whether they should bid.
When Monday arrived, Schaab gave his answer.
“It looks complicated,” he said. “I think it's about three to four times more difficult to do the radiological than what we're doing.”
Then he concluded, “But we can figure it out.”
The company ended up winning the $1.4 million contract.
“So all of a sudden, we get into nuclear, and it didn't bother me,” Schaab says. “The biggest challenge was learning all of the requirements.”
Ten years later, Schaab was feeling overworked from constant travel and too many projects.
“I left and started American DND with the intention of focusing primarily in the radiological, nuclear and fossil-power plant decommissioning,” he says. “At that time, 20 or so nuclear power plants were scheduled to be demolished, and I had one of the best resumes in the country for demolishing them.”
The Big Break
Bill Schaab, right, at Savannah River Nuclear Site demolition.American Demolition & Nuclear Decommissioning
“He was in charge of up to 110 men,” Schaab says, “and he did conventional and nuclear ordnance in the military. He had also rewritten procedures to make them more efficient and safer for the Navy.”
Sundeen decided to buy 51% of the company and became its president, CEO and treasurer. The company became a certified service-disabled veteran-owned small business.
Four years later, in 2010, the big break came.
It was a $4 million job to decommission the K Cooling Tower at the Savannah River Nuclear Site in Aiken, South Carolina. The tower was 455 feet tall, 330 feet in diameter and made of reinforced concrete.
American DND handled all the prep work for the implosion, with subcontractor Controlled Demolition Inc. (CDI) in charge of the explosives. It fell in 8 seconds after detonation, within its own footprint. It was the second-largest structure of its kind to be imploded.
The success of the project earned American DND 100% of the U.S. Department of Energy’s Safety Bonus Incentive Fee.
“That put us on the map,” Schaab says. “That made us who we are.”
A Most Contaminated Site
“This is the most contaminated open-air work going on in the country right now.” American Demolition & Nuclear Decommissioning
The West Valley Demonstration Project (WVDP) sits on 150 acres, 35 miles south of Buffalo and was the only commercial spent-nuclear-fuel reprocessing facility in the U.S. After operations ceased, the site was left with 640 metric tons of spent nuclear fuel and over 600,000 gallons of liquid high-level waste, according to the DOE. In 1980, Congress ordered DOE to clean up the site.
In 2011, American DND joined a consortium as a key subcontractor to demolish contaminated structures there.
Last December when Equipment World visited, American DND crews were demolishing an off-gas cell that had housed ventilation equipment for the Main Plant Processing Building.
“This is the most contaminated open-air work going on in the country right now,” said Sundeen, who oversees ADND’s work on the site.
“Nobody goes in or out of that area or moves inside there without our coordination. … Micromanage is the name of the game.”
“Mini Rainforest”
American DND developed water spray system on boom lifts to prevent airborne contamination at the West Valley Demonstration Project.American Demolition & Decommissioning
One such innovation, they call “turbine high lifts.” American DND and Holland High Lift, a local equipment dealer, replaced the work platforms on aerial boom lifts with water sprayers powered by generators. The sprayer-equipped lifts reach as high as 80 and 110 feet. They create a mist over the demolition site, while underneath, excavators break and remove pieces of the contaminated reinforced concrete that’s 2 to 5 feet thick.
“We basically create what we call a mini rainforest,” Schaab says.
The atomized water mist with surfactants attaches to radionuclides and carries them to the ground where fixatives are added to prevent them from going airborne.
The company also worked with OilQuick to engineer a system large enough for its excavator operators to change attachments without having to leave the cab. American DND uses excavators with pin sizes of 80 millimeters and up. When it came time to switch among shears, pulverizers and hydraulic hammers, it would take two to three workers in double hazmat suits and respirators three to eight hours to drive out the pins, which weigh 50 to 150 pounds each, and reinstall them.
Now it can all be done in less than a minute right from the cab without additional workers. The company saw a return on investment in three months, saving money and time and increasing safety. It later joined with OilQuick to demonstrate the system at the Waste Management Symposia in March in Phoenix to spread the word throughout the industry.
Bringing construction equipment into contaminated jobsites also requires lots of upfits to ensure safety. They have triple-plumb hydraulics, reinforced undercarriages and belly pans, cab guarding and sometimes HEPA filters for the cabs.
“Sometimes we'll put $150,000 to $200,000 of additional features and options on equipment that you wouldn't normally have on a standard digging excavator,” Schaab says. “That doesn't matter whether it's an excavator, a skid steer, a front-end loader, they all have these additional features and options.”
Repairing them is also complicated, as once they are in a contaminated area, special precautions must be taken. Technicians need to be double-suited with respirators, hoods, three pairs of gloves and other PPE.
“You have to get innovative,” Sundeen says. “You design ways to do it.”
A Culture of Safety
Bill SchaabEquipment World
Schaab and Sundeen believe safety starts with company culture that all leadership follows, which translates to the field. In developing a safety and health plan and considering safety practices, they get feedback from employees on what is working and what’s not.
Dan Stachelski, CIH, is ADND’s safety and health director and makes a point to travel to the various jobsites around the country to ensure stringent safety practices are being followed.
“I'm always out in the field,” Stachelski says. “I like to meet the people. I like them to bounce stuff off of me.”
“It really starts with a culture from the top down,” adds Schaab, who also travels frequently to sites to ensure safety.
Each day begins and ends with safety talks. Weekly and monthly safety meetings are also held. The company provides annual safety bonuses of up to $1,600 per employee who not only have no incidents but also participate in safety talks and in other ways.
The company performs in-house training and sends workers to third-party training. They will shut down a job for a day to focus on safety. They also give “lessons learned” talks gleaned from traveling their jobsites to share throughout the company.
Trenton Rodgers Norment, director of site operations at Four Rivers Nuclear Partnership in Paducah, Kentucky, recalls attending one of American DND’s safety celebrations for its employees.
“They were doing a post-job debrief and lessons to learn with their staff to go over things that they felt like could have been improved on for their next project,” he recalls. “I've never seen anything like that.”
“ADND makes safely performing work an absolute must,” says Kelly Wooley, CHBWV deputy general manager for the West Valley project. “The ADND leadership team provides technical guidance on how to safely execute our highly hazardous work. They also emphasize with their employees and our employees that safety is paramount to everything they and we do on site.”
The Next Generation
Blake Schaab at OilQuick with Hydraulic Coupler System in production for ADND's excavators.American Demolition & Nuclear Decommissioning
Nuclear decommissioning wasn’t his initial plan. He earned his captain’s license and worked on a 120-foot private yacht in the Bahamas and the Caribbean for a year and a half. But the Covid pandemic put an end to that career path.
American DND landed a large contract in Portsmouth, Ohio, at a site where uranium enrichment for U.S. nuclear weapons and commercial reactors occurred. Blake agreed to come aboard, expecting it to last about six months, after which he might go into commercial real estate.
“And then I really just ended up enjoying the work and enjoying what I was doing,” he says.
As vice president of finance and administration, he is spearheading efforts to streamline operations. He has brought in DocuWare software to make invoices all electronic and quick and easy for leadership to evaluate and approve.
The company is also working toward establishing Defense Contract Audit Agency (DCAA) status, which involves bringing in an independent, qualified accounting firm to audit the company’s accounting system to ensure it meets standards for handling government contracts correctly. That will allow the company to bid as a prime contractor on federal projects, enabling it to expand the business.
Blake and his father travel the U.S. and in Canada to the company’s various sites and to evaluate prospective projects. At 64, Schaab says he still enjoys the work and has no immediate plans to slow down. He also enjoys helping the radioactive-waste-management industry become more efficient, productive and safer.
“When we go to a site, we bring a wealth of knowledge and value, because we're doing this across the the nation,” he says. “We can then say, ‘Hey, there's a better way to do this, and we can prove it.’”
At American DND headquarters in New York, from left, Mary Curr, manager at Daniel P. Klos CPA PLLC; Linda Pauly, ADND general manager; Dan Stachelski, ADND safety and health director; Blake Schaab (on video conference screen); and Bill Schaab.Equipment World