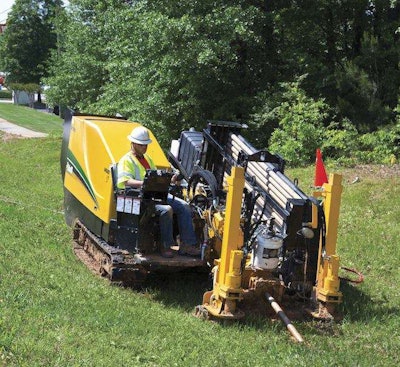
Intelligent hydraulic systems, telematics, configurable controls, standardization of controls and displays that can be customized from the type of information shown to colors displayed to units of measure are all appearing on drills. As the cost of these features continues to come down, they’re available on mid-level machines, not just the biggest and most expensive. Benefits include lower costs, greater productivity and better management of all resources from equipment to operators to drilling fluid.
Noise reduction continues
On Vermeer’s new S3 machines, sound has been decreased by at least 10 decibels. “That’s like taking your stereo from a 10 to a 5,” says Jon Kuyers, Vermeer senior global product manager for underground products. “Equipment will never be 100 percent silent, but we are making significant strides in sound reduction because contractors need to reduce their impact when working in more congested areas. Project owners are demanding quieter equipment on jobsites.” The D23x30 S3 has sound levels of 78 to 79 decibels at the operator’s ear.
Controllability
Drill operators use remote control to easily load and unload a drill off a trailer, and position it on site. Tethered remotes are common. Optional wireless remotes are increasingly popular as they further improve the safety and ease of these tasks.
Recognizing contractors need simplicity when training operators, many manufacturers have opted to use the same controls throughout their lineup, including Vermeer and Toro. Toro uses identical controls on both of their models, the DD2024 and DD4045 and the control pattern is switchable between single and double joysticks to suit operator preferences. The dual-joystick provides greater control while the single joystick is suited for simpler projects. says Josh Beddow, marketing manager. “By standardizing controls, the learning curve for operators is reduced or eliminated as contractors switch between classes of drills,” says Josh Beddow, marketing manager.
Digital displays make it easier to access needed information. The full CAN bus systems on Vermeer’s S3 machines monitor and collect information on all aspects of machine operation. The D24x40 S3 and larger models feature DigiTrak Aurora displays that integrate with the Vermeer InSite Productivity Tools suite (see story on page 71) to further enhance access to operating information. And operators aren’t the only ones seeking more information. “Real-time
Hydraulics
Advanced hydraulics allow OEMs to make significant changes to their machines. “Part of the objective is power in a small package,” says Matthesen. “Compactness and reduced weight improve transportability and site maneuverability and placement. Hydraulics are the key enabler.” The rotational drive system on the new Ditch Witch JT25 features a low-speed, high-torque motor that is smooth, quiet and efficient. The radial piston hydraulic motor allows changes in torque and speed with no planetary gearbox. Eliminating the planetary reduces cost, weight, frictional losses and heat. The drive design will be incorporated into other models.
Improved rotary hydraulics provide increased power to the rotary spindle on the new American Augers DD110 while using less engine horsepower. The rotary torque has been increased to 15,000 foot-pounds with this hydraulic rotation motor. American Augers developed a new rotary output gearbox to handle this increased power, and carriage speed has been increased from 100 to 170 feet per minute. “The net result is that the DD110 delivers more performance in a smaller package than the previous model,” says Richard Levings, American Augers product development manager.
Since hydraulics provide power for all machine functions, not just the actual boring process, smart hydraulics allow improvements in all areas of operation. Ground drive speed and power have been improved on most models of Vermeer HDDs with a redesigned hydraulic circuit, one proven on larger models of Vermeer drills, that makes more efficient use of horsepower. Barbco has expanded the use of their onboard programmable controller so operators can adjust the clamping force of the drill pipe break-out wrenches. This allows the use of a variety of drill pipe and down-hole tools without the risk of overclamping.
Choose wisely
With advancements occurring in all areas of HDD design, it’s important to consider all the factors when choosing a machine. “Get the right machine for the long term,” says Matthesen. “Spec for the bulk of the work you’ll be doing, not the exceptions. Look at the production amount, not just the dollar amount, of the initial investment. And don’t stop at the drill but consider the whole package, which includes the machine, trailer, tow vehicle, water and mud systems, and so forth.” He also says ergonomics help attract and retain the best talent. “It’s their office and operators appreciate a comfortable work environment.”
Beddow says the fundamentals are still important. “There’s no magic calculation that says exactly what piece of equipment will be perfect for every job, but there are a number of key pieces to consider when it’s time to make a choice.” He says questions that need to be addressed before making an equipment decision include:
• What is the total length of the run?
• What is the outer diameter of the pipe to run?
• What are the materials and ground conditions at the boring site (clay, soil, cobblestone, boulders, etc.)?
• Are there any challenges above ground to consider (tight spaces, traffic, fences, existing infrastructure, etc.)?
• What are the below ground conditions, such as variability in the substrate or hardness?
Levings says to look for equipment that doesn’t require permits and special transportation equipment to mobilize. As OEMs continue to pack more power into smaller packages, machines with higher thrust and pullback can be transported using standard trailers and tow vehicles.